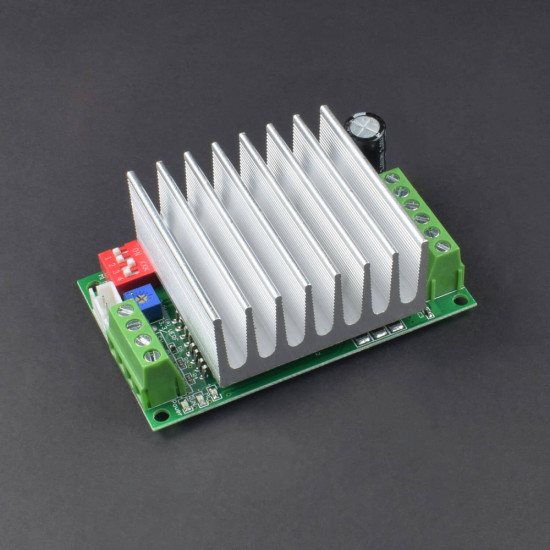
-550x550.jpg)

-80x80.jpg)
- Stock: In Stock
- Model: EVO-0907
- Weight: 95.00g
- Dimensions: 50.00mm x 82.00mm x 35.00mm
Description:
TB6600 stepper motor Driver Controller 4.5A 8~50V TTL 16 Micro-Step CNC Single-Axis Based on the TB6600HG chip, the new BL-TB6600-V1.2 driver model replaces the popular BL-TB6560-V2.0 driver. This driver controller is suitable for building not only amateur CNC systems but also professional ones based on high power engines. Compared to the previous generation of the TB6560AHG, the output of the TB6600HG has increased to 200W (as we see a practical doubling in power value), the operating voltage is raised from 35V (TB6560AHG) to 50V, the operating current is increased to 4.5A (5A peak value). The main aspects of this driver include intelligent current control and the use of PWM modulation, which makes it possible to connect stepper motors of any supply voltage and current to the driver – at a fixed level; the chip itself will limit the maximum current. The maximum operating frequency has been increased.
Specification:
Model: TB6600
Input Supply Voltage: 8 ~ 50V DC
Operating Voltage: 36V DC
Max. Output Current: 0.3 to 4.5A
Micro Step: 1, 2, 8, 16
Maximum PWM Frequency: 2000Hz
Hold Current Adjustment: 50% or 100%
Operating Temperature: -10 to 50°C
Features:
The output current is infinitely adjustable to meet your various application requirements.
Automatic half current function. And a semi-automatic flow switch, easy to use.
The use of high-speed optical coupling 6N137 ensures high-speed without losing a step.
Print on the back panel subdivides setup instructions.
Used to increase the heat sink, good heat dissipation.
Output short-circuit protection, the use of the mind.
Using common anode input mode, there are two input terminals, wiring more convenient.
Special note:
The power supply can not be reversed, otherwise will burn the chip.
Setting current should not exceed the rated current of the motor.
Instructions for use:
Operating voltage DC 10V-45V, it is recommended to use the switching power supply DC24V or DC32V power supply.
Two input terminals can only enter a group, two groups of terminals are identical, easy wiring.
Input pulse level is 5V, if 12V need a string of 1K resistance, if the 24V level, the need for a string of 2.4K resistance.
When CLK has a pulse, the motor is running, no pulse will automatically enter the set half-flow state, lock the motor.
When DIR low level or floating, the motor is forward, high-level reversal.
When EN low-level input or floating, will normal working, high level offline.
The white 4PIN bayonet terminal can be connected directly to the MKS-Gen's signal output (note the direction).
Unlimited Blocks, Tabs or Accordions with any HTML content can be assigned to any individual product or to certain groups of products, like entire categories, brands, products with specific options, attributes, price range, etc. You can indicate any criteria via the advanced product assignment mechanism and only those products matching your criteria will display the modules.
Also, any module can be selectively activated per device (desktop/tablet/phone), customer login status and other criteria. Imagine the possibilities.